Technology
A new iron age
For centuries, iron has been made the same way, using coal and extreme heat, and releasing gigatons of carbon dioxide emissions in the process.
At Electra we're reinventing this age-old process with our patented low-temperature electrochemical-hydrometallurgical system to refine ore into high-purity clean iron.
How Electra's process works
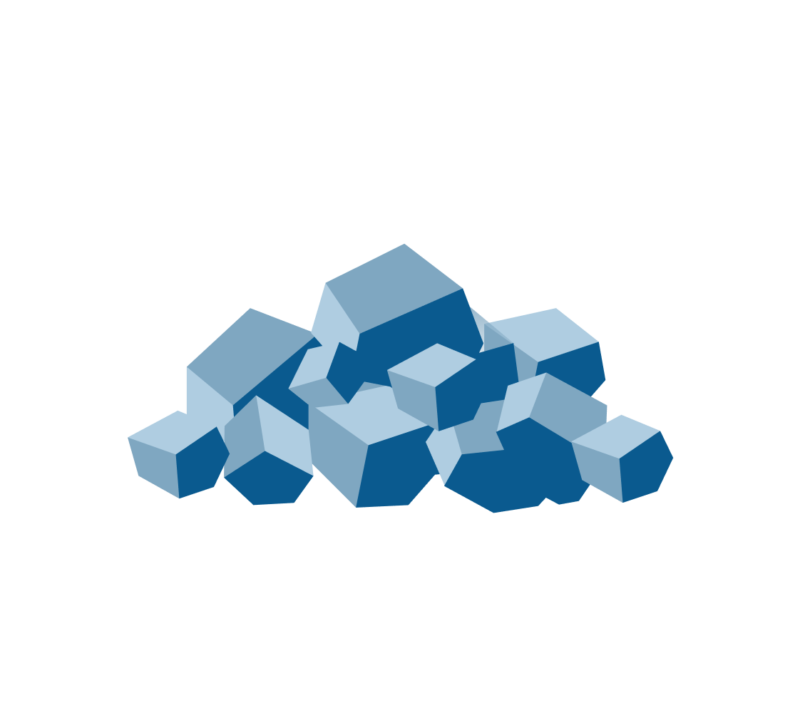
Iron ore is dissolved in an acidic solution.
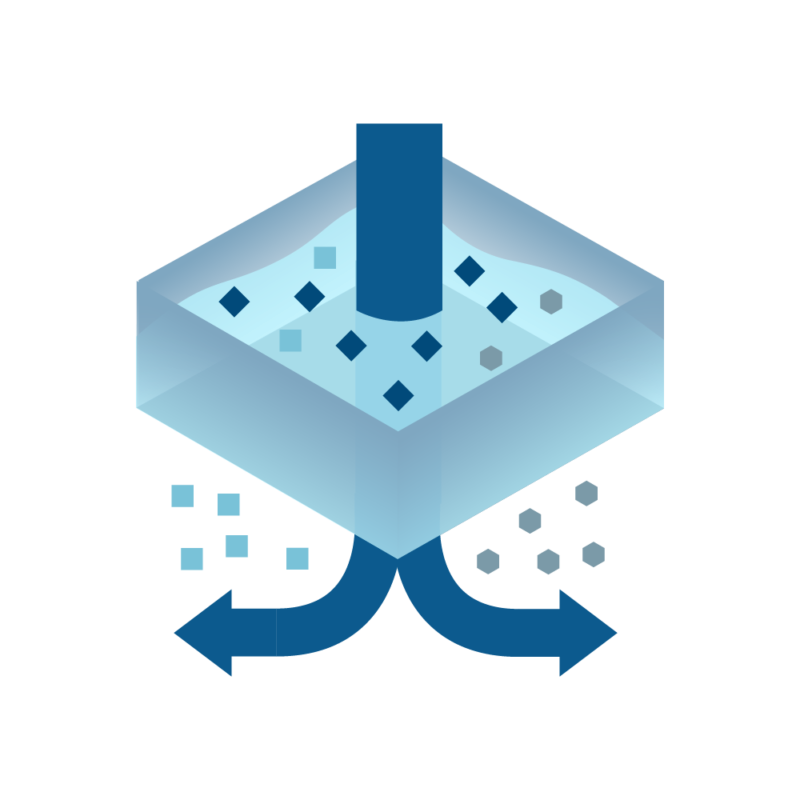
Iron is retained in the solution as co-products are collected and removed, while regenerating the acid.
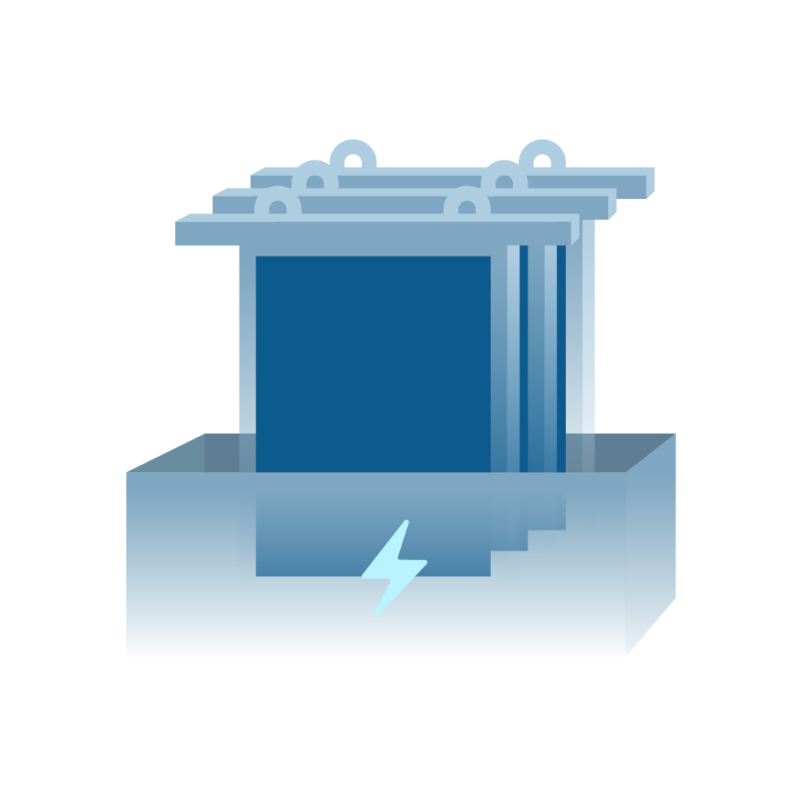
Electricity is run through the solution and iron is electrodeposited onto metal sheets.
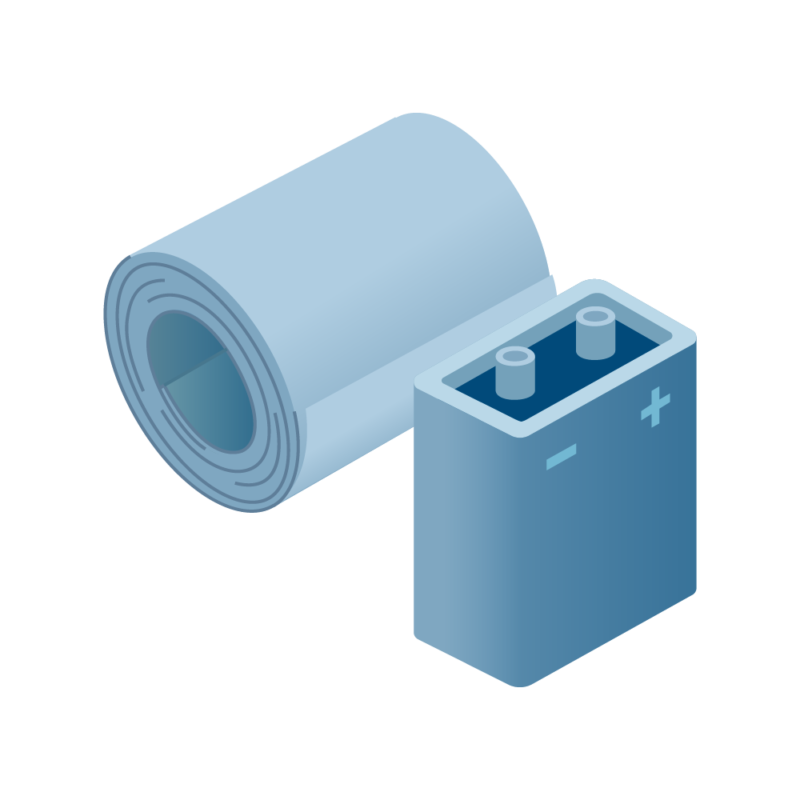
Electra's iron can be converted into steel using Electric Arc Furnaces (EAFs) or utilized to make iron-based batteries.
What makes Electra’s clean iron different?
Flexible Inputs
Compatible with intermittent renewable energy
Our low-temperature process allows us to synchronize production with the availability of cost-effective intermittent renewable energy.
Uses the widest range of iron ores
Traditional ironmaking uses the highest grades of ore as feedstock. Our process unlocks new types of ores including previously mined, unused materials.
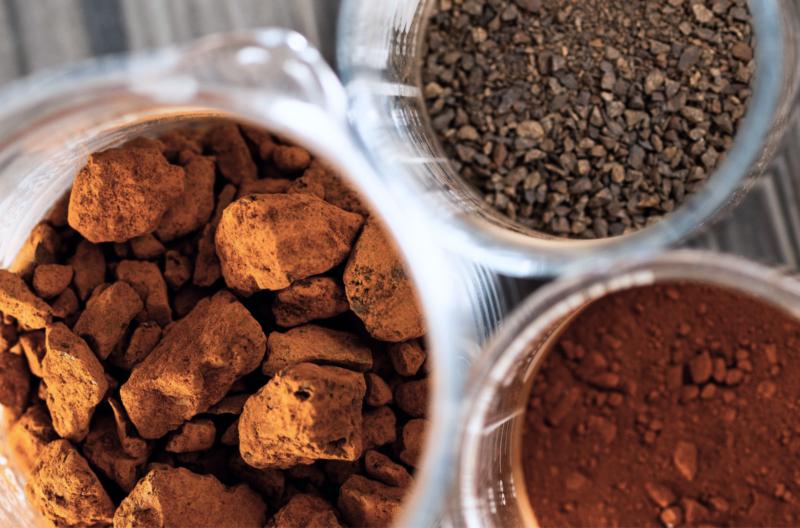
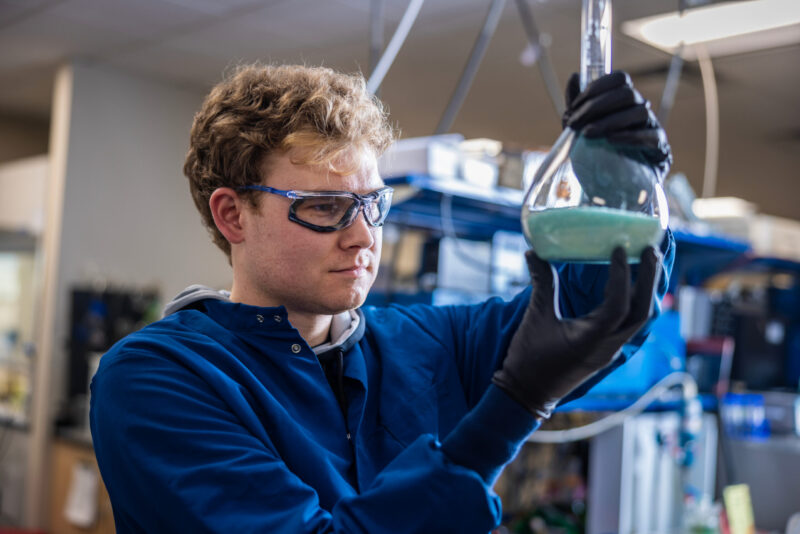
Valuable Outputs
Produces 99% pure iron
Our high-purity iron provides the highest economic value for EAF steelmakers and battery manufacturers.
Extracts co-products to maximize value
Our full value refining process removes co-products like silica and alumina, reducing waste and preserving critical minerals.
Modular Design
Our system is built in a network of connected cells — similar to stackable blocks — that can be replicated and combined to rapidly increase production.
Each repeatable, modular unit is built using readily available equipment and materials available at scale. This nimble, cost-effective approach is engineered for global scalability and commercial viability.
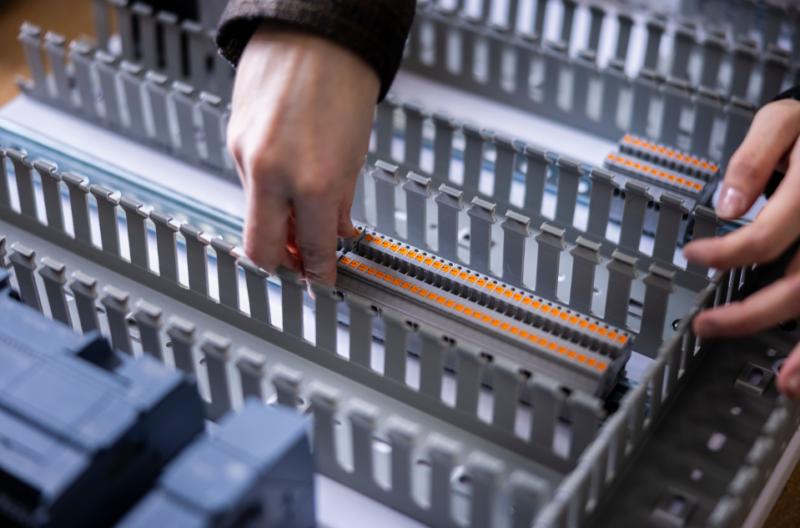
Recognized in the industry
Learn more about us
Meet the team
Our Team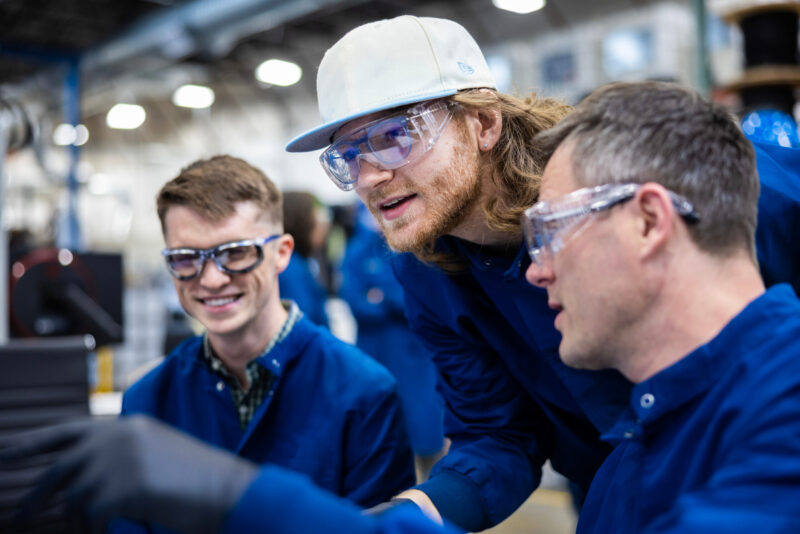